In previsione della fusione aziendale avvenuta a inizio gennaio, Altair Chemical ha redatto il suo…
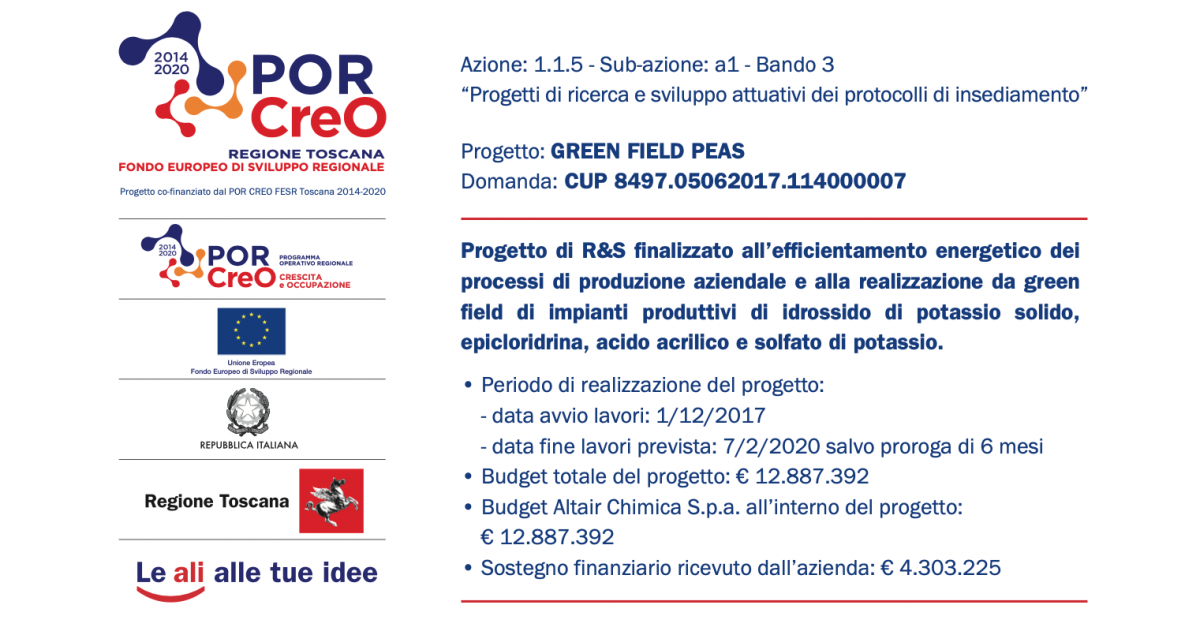
ALTAIR CHIMICA ha presentato in data 4/8/2017 domanda di contributo nell’ambito del bando per Progetti di Ricerca e Sviluppo della Regione Toscana (all’interno del Programma Operativo Regionale Crescita e Occupazione) e dell’Unione Europea (attraverso il Fondo Europeo di Sviluppo Regionale) per la realizzazione del progetto G.R.E.E.N. FIELD PEAS: si tratta di un progetto di Ricerca e Sviluppo (R&S) finalizzato all’efficientamento energetico dei processi di produzione aziendale e alla realizzazione da green field di impianti produttivi di idrossido di potassio solido, epicloridrina, acido acrilico e solfato di potassio. Il progetto, avviato da Altair Chimica il 1° Dicembre 2017, è stato ammesso al finanziamento in data 7/02/2018.
Il progetto G.R.E.E.N. FIELD PEAS, POR CreO FESR Toscana 2014/2020 Azione 1.1.5 – Sub Azione a1 – “Progetti di ricerca e sviluppo attuativi dei Protocolli d’insediamento” (Bando 3), consiste di 7 linee progettuali o sotto-progetti:
- R&S di Tecnologie Innovative volte all’ottenimento di un importante recupero di CO2 e calore nel processo produttivo del carbonato di potassio, finalizzato al riutilizzo della CO2 di uscita dal cogeneratore per produrre K2CO3
- R&S delle caratteristiche tecniche ed operative di un innovativo bruciatore bi-fuel metano-idrogeno
- R&S di un innovativo impianto, da green field, per la produzione di epicloridrina, partendo da feedstock presenti in Altair Chimica o facilmente reperibili in filiera corta, da sotto-produzioni di bio-carburanti
- R&S di un sistema di gestione integrata ed ottimizzazione dei processi di produzione e consumo di idrogeno e cloro a seguito della messa in marcia del nuovo impianto di produzione di Soda caustica – Progetto SODA-4.0 (Sistema di Ottimizzazione e Decisione Automatizzata 4.0)
- R&S di un innovativo impianto di produzione di solfato di potassio
- R&S di un innovativo impianto di produzione di idrossido di potassio solido, partendo dalla soluzione acquosa al 50%, già presente in stabilimento
- R&S di un impianto di autoproduzione di energia elettrica da fonte rinnovabile (geotermica o idroelettrica) o da fonte fossile a basso impatto ambientale, ad altissimo rendimento (co-generazione con gas naturale).
In budget totale del progetto, che dovrebbe concludersi nel corso del 2020, è di 12.887.392 €: il sostegno finanziario concesso d Altair Chimica è di 4.303.225 €.
Per quanto riguarda in particolare il Progetto SODA-4.0, questo ha l’obiettivo di sviluppare ed implementare un sistema di gestione integrata ed ottimizzazione dei processi di produzione e consumo di idrogeno e cloro a seguito del nuovo assetto produttivo di Altair che si è realizzato con la messa in marcia del nuovo impianto di produzione di NaOH (Soda caustica): consiste in sintesi nella realizzazione di un sistema robotizzato/ automatizzato capace di interfacciare tutte le informazioni presenti nel DCS (Distributed Control System o Sistema di Controllo Distribuito) e nel gestionale aziendale e di prendere le decisioni ottimali in termini di produttività, consumi energetici e di effettuare le operazioni con il massimo grado di sicurezza possibile, andando sempre ad effettuare operazioni perfettamente codificate, senza commettere errori umani e/o dimenticanze varie.
Nello specifico il sistema di ottimizzazione avrà come input la produzione richiesta di KOH, di K2CO3, di KOH solida, di NaOH e dei prodotti clorurati, oltre che il costo energetico delle varie ore in cui avranno corso le produzioni (PUN, prezzo Unitario Nazionale dell’energia elettrica) e dovrà fornire, in tempo reale (Real Time Optimization), la modulazione della marcia degli impianti produttori di cloro (le celle elettrolitiche) e utilizzatori di cloro (cloroparaffine, ipoclorito di sodio, cloruro ferrico tecnico, cloruro ferrico e ferroso qualità potabile e acido cloridrico), per avere in output tutto quanto necessario all’espletazione degli ordini clienti al minor costo energetico possibile all’interno del periodo produttivo necessario a farlo. L’acquisizione di tutti i dati necessari, sia da parte del DCS per i dati di produzione, sia dall’AS400 (dati commerciali), sia Energetici (piattaforma web sul PUN del GSE), avverrà attraverso l’utilizzo di una piattaforma snap4city, che dovrà essere capace di ricevere, tramite una connessione dinamica appositamente sviluppata fra DCS, web e sistema di gestione AS400, tutti i dati provenienti dall’impianto attraverso le strumentazioni interfacciate con il DCS e con tutti i dati provenienti da AS400, come per esempio gli ordini dei clienti e con le info energetiche necessarie per ottimizzarne il costo energetico. Si potrà anche prevedere un ulteriore connessione che permetta al sistema di gestione AS400 di ricevere in automatico gli ordini dei clienti, evitando la fase di immissione manuale degli stessi, attualmente in essere. Tale possibilità andrà prevista nello sviluppo degli algoritmi e delle varie routine da sviluppare, ma richiederà l’ausilio di clienti disponibili a tale sviluppo, pertanto si articolerà successivamente al rilascio del presente progetto.
La piattaforma acquisirà i dati di input dal DCS e fornirà i suoi output al DCS stesso, attraverso le routine sviluppate nell’RTO; pertanto il sistema di ottimizzazione occuperà un layer gerarchicamente superiore al DCS ed opererà quindi come un “operatore automatico”.
Il sistema RTO calcolerà l’assetto di marcia degli impianti produttori e consumatori di cloro attraverso la risoluzione di un problema di ottimizzazione vincolata lungo un opportuno orizzonte temporale, tenendo conto di modelli di bilancio di materia ed energia degli impianti, dei vincoli di marcia minima e massima degli impianti, degli stoccaggi disponibili nello stabilimento, del costo energetico orario e degli interblocchi già presenti sugli impianti in termini di processo e sicurezza.
Il sistema potrà funzionare in due modalità:
- modalità background (supporto alla decisione): il sistema RTO, acquisiti i dati, elabora gli assetti ottimali di marcia degli impianti e li propone all’operatore che poi deciderà quali valori di assetto utilizzare; i valori proposti vengono comunque storicizzati dal DCS;
- modalità online (decisione automatica): il sistema RTO, acquisiti i dati, elabora gli assetti ottimali di marcia degli impianti e li “scrive” in tempo reale sul DCS operando quindi in maniera automatica sul controllo di processo e produzione.
La modalità background sarà usata in una prima fase di commissioning al fine di convalidare la correttezza di funzionamento del sistema RTO e al fine di individuare modifiche e miglioramenti necessari. Una volta ritenuto affidabile, il sistema verrà passato in modalità online per un periodo di ulteriore convalida ed affinamento, ottenendo infine il sistema RTO definitivo, che opererà in automatico. Ovviamente, l’operatore potrà in qualsiasi momento passare dalla modalità online a quella background e viceversa, garantendo quindi la perfetta resilienza del sistema di controllo a fronte di possibili malfunzionamenti.
Dal momento in cui il sistema RTO entrerà in funzione, sulla piattaforma verranno implementate tutte le logiche e le routine necessarie alla produzione di statistiche e di analisi dei big data che verranno continuamente registrati dall’impianto e dal sistema gestionale, così da poter disporre di tutti i dati di input da fornire ad algoritmi di autoapprendimento, per alimentare automaticamente il miglioramento delle performance complessive del sistema 4.0, attraverso nuovi o migliori comandi da restituire sia al DCS che ad AS400.
Aspetti d’Innovatività del presente progetto
Al momento attuale non esistono stabilimenti cloro-soda o cloro-potassa che vadano oltre alla presenza di una sala quadro con DCS, più o meno completo in termini di strumentazione interfacciata. Ad oggi il massimo livello di automazione si ferma a questo livello, nel quale è prevista la presenza del quadrista in Control Room e la presenza di operatori esterni, pronti ad agire in base alle operazioni necessarie per la regolazione delle varie produzioni. Oggi, dovunque si trovi un cloro-soda o un cloro potassa nel mondo, le decisioni sugli assetti produttivi dei vari reparti, vengono decisi da sistemi gestionali più o meno complessi, che trasferiscono il proprio output ai vari responsabili di pianificazione della produzione, che, a loro volta, mediando tra le esigenze commerciali e le esigenze produttive, stabiliscono quali informazioni far pervenire al quadrista, il quale, finalmente darà ai suoi uomini e al DCS le istruzioni per far marciare la produzione nella direzioni decisa.
Tali input hanno due ordini di problemi: risentono di eventuali errori umani di valutazione, di eventuali dimenticanze in alcuni elementi della catena decisionali e risentono della possibilità di errore nell’effettuare tutte le manovre necessarie per far andare tutto l’impianto secondo i desiderati teorici.
Trovate tutti i dettagli del progetto qui.