In previsione della fusione aziendale avvenuta a inizio gennaio, Altair Chemical ha redatto il suo…
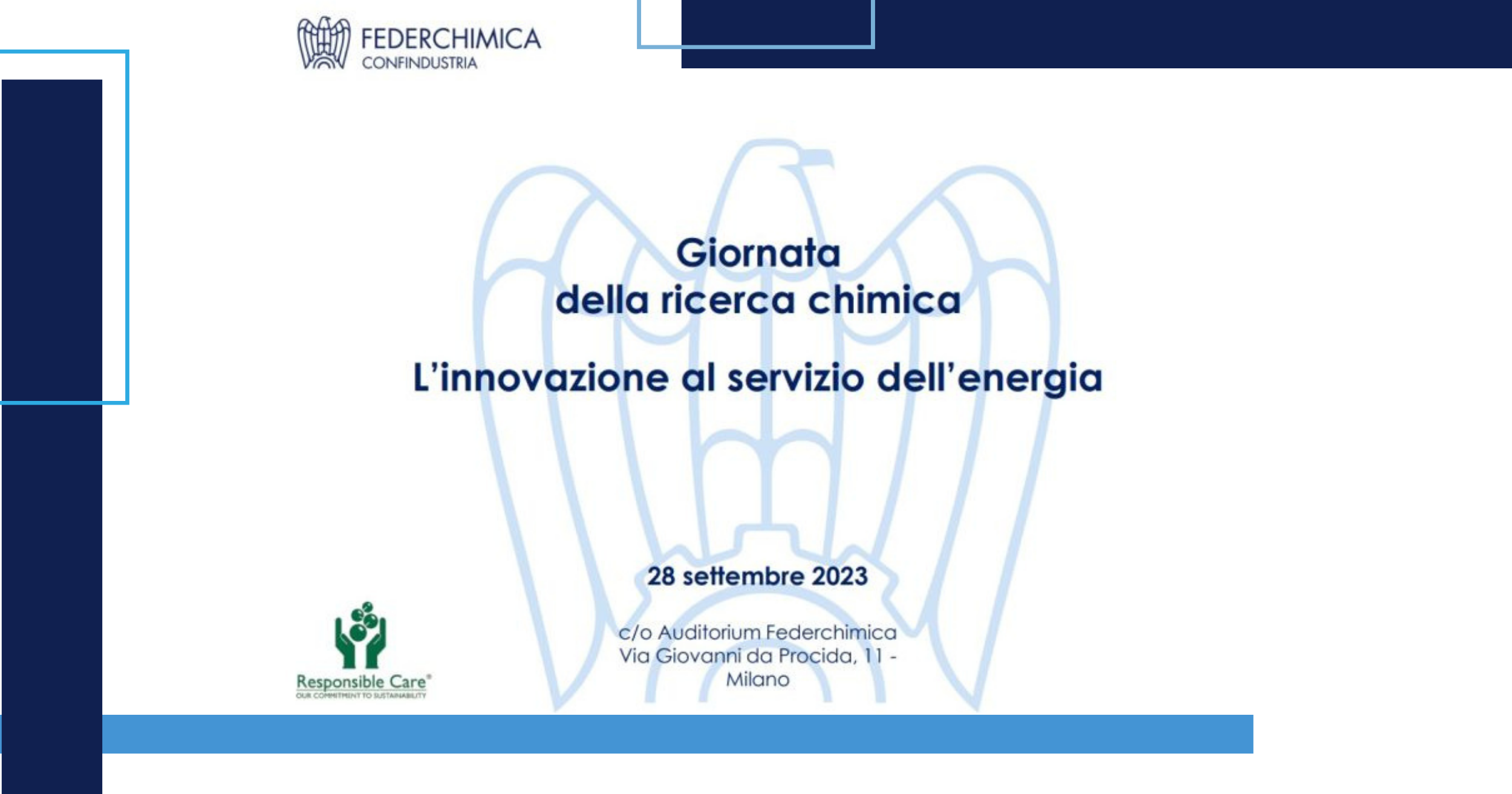
La crisi energetica generatasi nella ripresa post-pandemica ha reso ancor più impellente il raggiungimento di un sempre maggiore grado di efficienza energetica per l’industria chimica, altamente energivora. Un percorso che vede Esseco Industrial protagonista da anni, attraverso diversi progetti di ricerca e sviluppo in collaborazione con dipartimenti universitari selezionati e centri di ricerca accreditati.
Proprio per analizzare e diffondere buone pratiche e progettualità, Federchimica-Confindustria celebra oggi – 28 settembre – a Milano la “Giornata della ricerca chimica” dedicandola a “L’innovazione al servizio dell’energia”. Imprese, università e centri di ricerca a confronto sulle innovazioni in campo energetico per il settore della chimica. I ricercatori lavorano da tempo all’efficienza accumulativa e distributiva, a nuovi materiali e soluzioni, all’idrogeno come nuovo vettore e alla decarbonizzazione in generale, giocando un ruolo fondamentale negli obiettivi di decarbonizzazione al 2050. Tre i focus della giornata: elettrolisi, batterie ad alte prestazioni e biocarburanti.
Entriamo nel dettaglio dei progetti R&S in corso di realizzazione o già giunti a conclusione nelle società di Esseco Industrial.
Dopo aver storicamente utilizzato l’ingente emissione di calore della produzione di anidride solforosa da zolfo per produrre vapore ad alta pressione e fornire energia all’intero stabilimento, in Esseco Srl abbiamo investito 40 milioni di euro per rinnovare l’impianto di produzione di sodio idrosolfito (SHS) grazie al quale abbiamo ridotto i costi di smaltimento delle acque reflue, efficientando l’intero processo. Con un gruppo elettrogeno di trigenerazione alimentato a metano, diamo vapore all’impianto e convogliamo l’acqua fredda abbattendo i consumi elettrici. Inoltre, solo pochi giorni fa, abbiamo candidato ad un bando della Regione Piemonte un nuovo progetto di efficientamento. Con il dimezzamento della temperatura dei gas in uscita dal forno di combustione dello zolfo – da 300° a 150° C – recupereremo una ulteriore quota di vapore che, attraverso una nuova turbina, produrrà 1.600 MWh di energia aggiuntiva. Anche la grande attenzione al patrimonio idrico ci ha spinto a guardare in questa direzione e a ragionare ad una soluzione per la riduzione del prelievo di acqua da pozzo. Con l’introduzione di un gruppo frigorifero abbinato a un air cooler di pre-raffreddamento abbatteremo i consumi idrici del 90% circa dell’impianto oggetto della modifica, contribuendo così alla sostenibilità ambientale ed economica.
In Altair Chimica, per valorizzare energeticamente al massimo l’idrogeno derivante dal processo industriale, abbiamo in passato ricercato e installato un primo generatore di vapore bi-fuel prototipo e in seguito abbiamo avviato uno studio di ricerca con UNIFI REASE che ha portato all’installazione di una nuova caldaia che, con la tecnologia full idrogeno per la produzione di vapore, ha permesso di abbattere i consumi di metano. A ciò si è aggiunto il progetto di R&S con l’Istituto di Geoscienza e Georisorse di Firenze volto ad individuare il metodo di autoproduzione di energia elettrica più energeticamente efficiente ed ambientalmente sostenibile per la nostra società: da qui sono scaturiti gli impianti fotovoltaici installati nello stabilimento e sono state gettate le basi per future ricerche in ambito geotermico. Perseguendo l’ambiziosa strada delle energie rinnovabili siamo poi arrivati alla stipula del primo contratto Power Purchasing Agreement (PPA) ea alla decisione di realizzare importanti investimenti in energia solare extra situ.
La collaborazione con ICCOM-CNR e il dipartimento di Ingegneria dell’Università di Firenze ha visto concretizzarsi l’investimento di 14 milioni di euro per una nuova linea di elettrolisi con un aumento del 50% della produttività dell’impianto e consumi elettrici più performanti.
Nell’ambito del controllo delle emissioni di gas serra e cattura e riutilizzo della CO2, il più importante investimento realizzato dalla società ha riguardato l’installazione di un impianto di recupero CO2 e calore dai fumi della cogenerazione ad alto rendimento da 4,6 MWe finalizzato alla produzione del carbonato di potassio (K2CO3). Questo progetto di cattura e utilizzo della CO2 dei fumi per la produzione di carbonato ha permesso di abbattere in parte le emissioni del cogeneratore stesso. Si sta oggi proseguendo sulla strada di questo vincente progetto, prevedendo di realizzare un analogo recupero dai fumi di combustione del nuovo cogeneratore installato, con un obiettivo di aumento del 50% della cattura della CO2.
In Hydrochem, con un ambizioso progetto di rilancio industriale, in corso dall’acquisizione dello stabilimento nel 2019, abbiamo installato un nuovo processo di elettrolisi a membrane rientrante nelle BAT (Best Available Technologies) europee introducendo, nello stesso, nuovi sviluppi in grado di superare lo stato dell’arte raggiunto in precedenza a livello internazionale e di gruppo. Siamo riusciti, inoltre, a trovare le soluzioni impiantistiche per garantire la più alta flessibilità possibile dei carichi produttivi: in questo modo, sfruttiamo al meglio l’energia proveniente dalle due centrali idroelettriche al servizio dello stabilimento e diminuiamo l’assorbimento di energia di rete.
Nuove progettualità saranno presto messe in cantiere per ulteriori innovazioni in campo energetico, grazie alla collaborazione con università e centri di ricerca accreditati. R&S che sosterranno l’ambizioso percorso di Esseco Industrial verso l’abbattimento delle emissioni legate al proprio fabbisogno elettrico: ad oggi, abbiamo già raggiunto il 50% di energia rinnovabile.